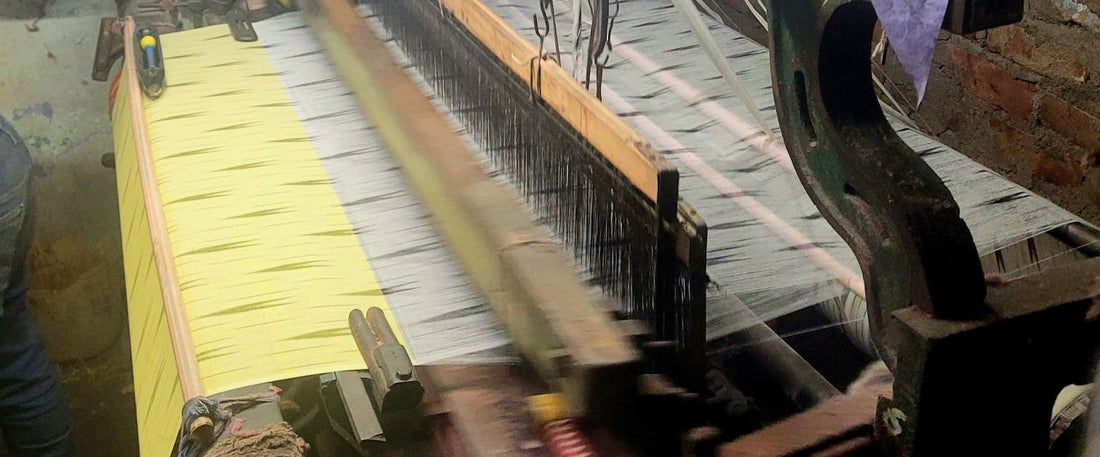
Exploring the Art of Hand-Painted Madhubani Sarees and the Tussar Silk Industry in Bhagiya and Bhagalpur
Share
A Journey Through Art, Culture, and Weaving Traditions
India’s rich textile heritage isn’t just about fabrics—it’s about stories, traditions, and the artisans who keep them alive. My recent journey through Bhagiya (Jharkhand) and Bhagalpur (Bihar) took me deep into the world of Hand-Painted Madhubani Sarees and the legendary Tussar Silk Industry. More than just witnessing these art forms, I got to experience them firsthand—walking through the narrow village lanes, meeting the artisans, and seeing centuries-old craftsmanship unfold before my eyes.
Bhagiya, Jharkhand – The Hidden Gem of Hand-Painted Madhubani Sarees
Tucked away in rural Jharkhand, Bhagiya isn’t a place you’ll find on most tourist maps, but it holds a priceless artistic heritage. While Madhubani art is traditionally associated with the town of Madhubani in Bihar, my research led me here—where I discovered a thriving community of artisans working with Tussar silk and hand-painted sarees.
Getting There – A Ride Down Memory Lane
My adventure began with the Vande Bharat Express to Bhagalpur, followed by a local train to Mirza Chowki—the nearest railway station. The last leg? A bumpy auto-rickshaw ride, squeezed into the front seat, dodging potholes, and holding on for dear life as my daredevil driver sped through half-constructed roads. It felt like a throwback to childhood—an experience that was equal parts thrilling and nostalgic.

Meeting the Artisans of Bhagiya
Upon reaching Bhagiya, I was greeted by Udit, a passionate young entrepreneur in his mid-20s, continuing his family’s Tussar silk business. His father, a master weaver himself, warmly welcomed me and introduced me to Gichha Tussar silk—a unique variant known for its rich texture and durability.
The Process of Creating a Hand-Painted Madhubani Saree
Walking through Bhagiya’s narrow lanes, I saw women seated in sunlit courtyards, carefully spinning yarn from cocoons—a sight that made me pause and take it all in. Almost every household had a handloom, and unlike the looms I’d seen in my childhood, these were set in sunken pits, allowing artisans to sit comfortably as they meticulously wove their magic into the fabric. Watching this age-old process live was nothing short of mesmerizing.
Udit’s brother-in-law took us on a tour of the village, where I witnessed every intricate step of saree-making—dyeing, hand-painting, ironing—each stage a labor of love. It takes nearly two weeks for a saree to go from raw silk to a finished masterpiece.

The themes of their artwork are deeply rooted in mythology, nature, and folklore—Krishna playing the flute, Lord Ram and Sita, dancing peacocks, intricate fish patterns, celestial motifs—all meticulously hand-drawn and brought to life with vibrant natural colors. Unlike machine-printed textiles, every brushstroke tells a story, making each saree one of a kind.
Today, Bhagiya’s Madhubani sarees are gaining recognition across India and the world, thanks to the resilience of artisans who refuse to let their heritage fade into history.
Bhagalpur, Bihar – The Silk City of India
After an incredible time in Bhagiya, I hopped back on the local train to Bhagalpur, famously known as the "Silk City of India". Here, the Tussar silk industry has flourished for centuries, producing some of India’s most sought-after fabrics—renowned for their natural sheen, rich texture, and earthy elegance.
The Making of Bhagalpuri Tussar Silk
The journey of Bhagalpuri Tussar silk begins in the forests of Jharkhand and Bihar, where silkworm cocoons are carefully harvested. Unlike traditional silk, Tussar silk has a coarser texture and a natural golden sheen, giving it a distinct rustic charm.
A Tour Through Bhagalpur’s Silk Industry
I was lucky to have Aniket—a young entrepreneur juggling his studies while starting his own Tussar saree business—as my guide. Riding pillion on his motorbike, we weaved through Bhagalpur’s bustling streets, heading towards Champanagar, a renowned hub for Tussar silk production.
Unlike Bhagiya’s handloom-dominated setting, Bhagalpur has embraced power looms, which run 24/7, producing 6–10 sarees per day, depending on the thread count and yarn quality.
Experiencing the Power Loom Workshops
Stepping into a power loom workshop was like entering another world—a symphony of rhythmic clattering, as threads intertwined at an astonishing speed. Though the noise was deafening, watching intricate designs emerge from the looms in real-time was truly fascinating. Aniket walked me through the different types of Tussar silk—from Desi Tussar to Tussar-by-Tussar—each with its unique texture and character.
A Lesson in Saree Shopping
To cap off the day, Aniket invited me to his sister’s house, where I was treated to chai and local snacks—a small but heartwarming moment that made me feel at home. Later, I visited a mall to see how hand-painted sarees were being sold.
To my surprise (and slight amusement), a salesman tried to pass off screen-printed sarees as hand-painted originals! I couldn’t help but smile—Nice try, but after my crash course in handloom weaving and Madhubani painting, you can’t fool me now!
The Fusion of Madhubani and Tussar Silk – A Timeless Masterpiece
One of the most breathtaking discoveries of my trip was the fusion of hand-painted Madhubani art on Bhagalpuri Tussar silk. This combination of two heritage-rich crafts results in sarees that are not just garments but living pieces of history.
Owning one means carrying forward an artistic legacy—a tradition woven with care, culture, and craftsmanship.
Preserving the Art and Empowering Artisans
Despite their beauty and significance, both the Madhubani saree industry in Bhagiya and the Tussar silk industry in Bhagalpur face serious challenges—machine-made alternatives, unfair pricing, and the declining artisan community.
While these sarees fetch high prices in international markets, the artisans behind them rarely see financial improvement.
At CREATUNIQ, we aim to change that by bringing these exquisite handcrafted sarees to a global audience—ensuring that artisans receive the recognition and fair compensation they truly deserve.